Pump Problems: Suction Loss
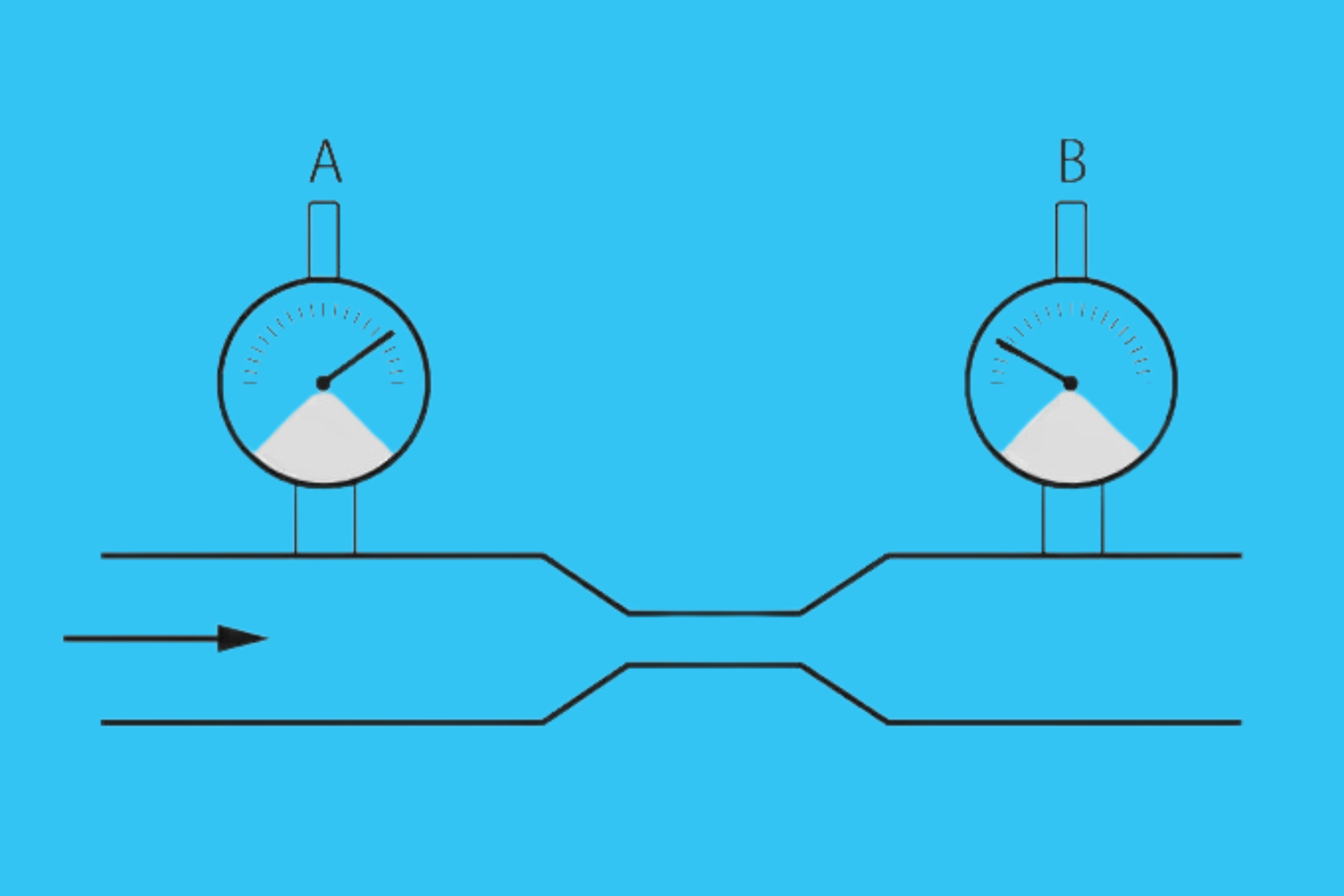
Efficient pump operation is essential for the smooth running of various processes, from industrial applications to residential systems. By understanding the causes of suction loss, including cavitation, poor pipe design, and inadequate pump positioning, you can take proactive steps to mitigate these issues and ensure optimal pump performance. We will explore techniques such as proper pump selection and installation, regular maintenance protocols, and the use of advanced technologies to combat suction loss effectively.
Pumps play a crucial role in various industries, from water treatment plants to oil refineries. Understanding how pumps work and the factors that can affect their performance is essential for optimizing their efficiency. One common challenge that affects pump performance is suction loss. Suction loss occurs when there is insufficient suction pressure at the pump inlet, leading to decreased flow rates and increased energy consumption.
There are several factors that contribute to suction loss, including cavitation, poor pipe design, and inadequate pump positioning. Cavitation occurs when the pressure at the pump inlet drops below the vapor pressure of the liquid being pumped, causing the formation of vapor bubbles. These bubbles then collapse when they reach an area of higher pressure, resulting in damage to the pump impeller and reduced performance. Poor pipe design, such as excessive bends or undersized pipes, can cause frictional losses and reduce the available suction pressure. Additionally, improper pump positioning, such as placing the pump too far above the liquid source, can lead to inadequate suction pressure.
To overcome suction loss challenges, it is crucial to identify the root causes and implement appropriate strategies. In the following sections, we will discuss the impact of suction loss on pump efficiency and explore techniques for minimizing suction loss in pump systems.
Suction loss can have a significant impact on pump performance, leading to several challenges that can affect the overall efficiency and reliability of the system. Understanding these challenges is essential for implementing effective solutions.
One of the main challenges caused by suction loss is decreased pump efficiency. When the pump is not receiving sufficient suction pressure, it needs to work harder to maintain the desired flow rate. This results in increased energy consumption and higher operating costs. Additionally, decreased pump efficiency can lead to reduced flow rates, which can negatively affect the overall process performance. For example, in water treatment plants, lower flow rates can result in inadequate water supply, affecting the quality and availability of treated water.
Another challenge associated with suction loss is increased maintenance requirements. When pumps operate under conditions of low suction pressure, they are more prone to cavitation and damage to the impeller. This can lead to frequent breakdowns and the need for costly repairs or component replacements. Increased maintenance requirements not only result in higher expenses but also cause downtime, which can disrupt the entire system's operation.
Minimizing suction loss in pump systems requires a comprehensive approach that addresses the root causes and implements effective strategies. By adopting the following techniques and best practices, you can optimize pump performance and ensure smooth operation.
Proper pump installation and maintenance are crucial for maximizing pump performance and minimizing suction loss. By following industry best practices and adhering to recommended maintenance protocols, you can ensure the longevity and efficiency of your pump system.
During the installation process, several factors should be considered to minimize suction loss. Proper positioning of the pump relative to the liquid source is essential to ensure adequate suction pressure. Ensure that the pump is located at an optimal height and that the suction pipe is properly sized and supported. Avoid excessive bends and use smooth pipe materials to minimize frictional losses. By paying attention to these installation details, you can prevent common suction loss issues from arising.
Regular maintenance is equally important for preventing suction loss and ensuring optimal pump performance. Develop a comprehensive maintenance plan that includes routine inspections, cleaning, lubrication, and component replacements as needed. Regularly monitor the pump system for any signs of wear or damage and address any issues promptly. By maintaining your pump system in good working condition, you can minimize suction loss and extend the lifespan of your equipment.
Advancements in technology have led to the development of various tools and technologies for monitoring and optimizing pump performance. By harnessing the power of these innovations, you can proactively manage suction loss and ensure optimal pump operation.
Suction loss challenges can significantly impact pump performance, leading to decreased efficiency and increased maintenance costs. However, by implementing the best practices outlined in this article, you can overcome these challenges and achieve optimal pump performance.
Proper pump selection and installation, regular maintenance protocols, and the utilization of advanced technologies are key strategies for combating suction loss. By taking proactive measures to address suction loss issues, you can improve pump efficiency, minimize downtime, and save valuable time and money in the long run.
Remember, optimizing pump performance is an ongoing process. Regularly monitor your pump system, implement preventive maintenance measures, and stay updated on the latest advancements in pump technology. By doing so, you can ensure that your pumps operate at their peak performance, supporting the smooth operation of your processes and systems.
So, don't let suction loss challenges hold you back. Take control of your pump performance and maximize efficiency by implementing the strategies shared in this article. Happy pumping!
Call us on (02) 4271 2220
email us here or complete the order form below