Expert advice & Speedy Delivery
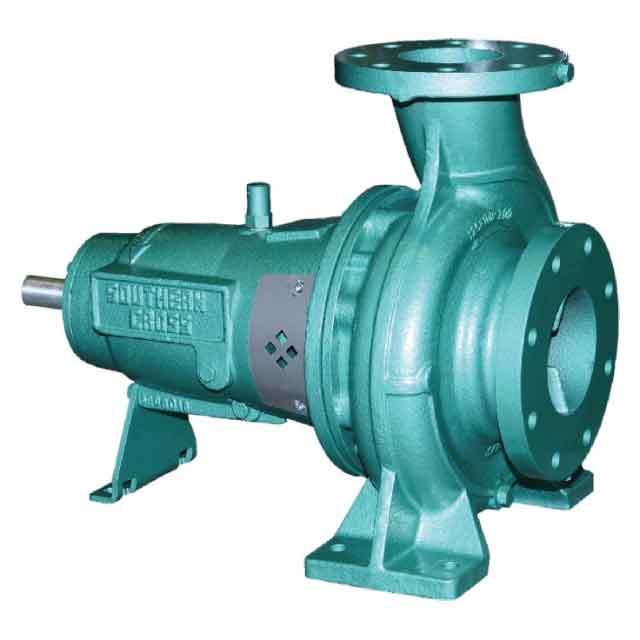
Centrifugal Pumps
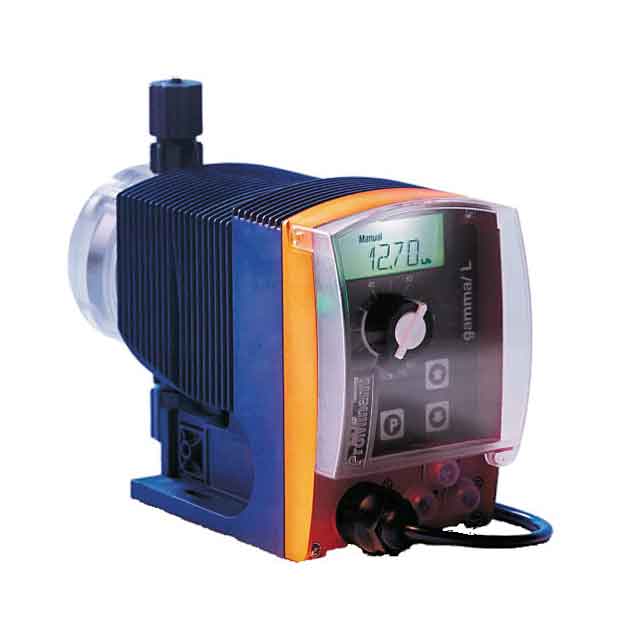
Metering Pumps
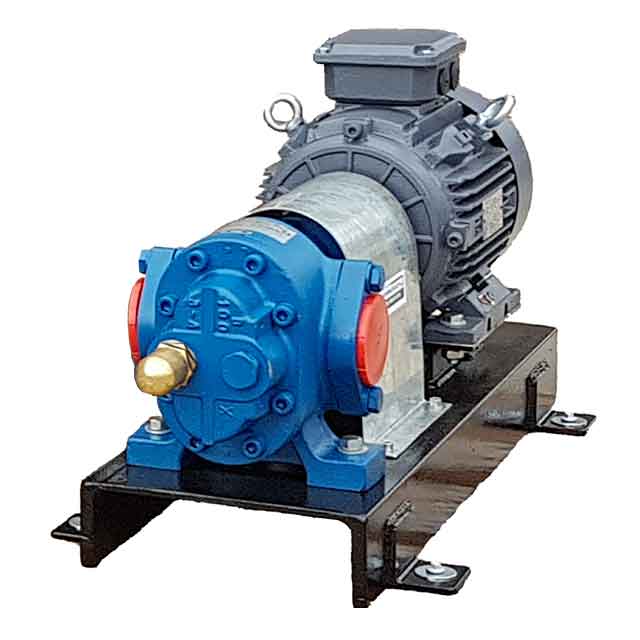
Gear Pumps
Air Operated Diaphragm Pumps, sometimes known as Pneumatic Diaphragm Pumps, AODD Pumps or AOD Pumps, can be used for multiple applications in the mining and industrial areas, as well as general plant service. Air operated diaphragm pumps are a type of reciprocating diaphragm pump which contains two diaphragms driven by compressed air. Air section with a shuttle valve applies air alternately to the two diaphragms. Each diaphragm has a set of check or ball valves.
The air operated diaphragm pump is especially serviceable in areas where electricity isn’t readily available, or in explosive or fl ammable situation. These air operated diaphragm pumps are also used for chemical transfer, de watering underground coal mines, the food manufacture industry or any application where the liquid being pumped has a high viscosity or high solid content.
Southern Pumping Specialists maintains strong product knowledge of Air Operated Diaphragm pumps and their application to the various industries they are particularly suited to. Selections, sales, spares and repairs of all makes and models is offered with confidence.

Centrifugal pumps are the most commonly used pump type in the world. A simple principle of increased fluid pressure from the pump inlet to its outlet is created by the transfer of mechanical energy from the drive or motor through the rotating impeller. The fluid moves from the inlet to the impeller and out via its blades. The centrifugal force increases the fluid velocity, here Kinetic energy is transformed to pressure.
Southern Pumping Specialists is experienced in the selection, specification, supply and repair of these pumps along with the design and construction of complete systems incorporating any number of centrifugal pumps.
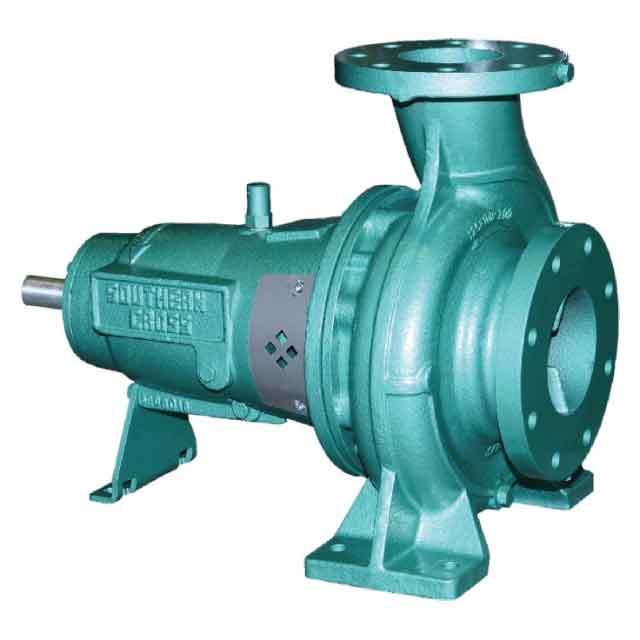
Gear pumps, a type of rotary positive displacement pump, which can transfer fluids of high viscosity at a high pressure, in a non-pulsating action. The fluid is transferred by gears coming in and out of mesh, creating a constant amount of fluid for each revolution.
Gear pumps are not suited to pumping solids, and abrasive liquids, but are well suited to handling liquids such as fuel and lubricating oils.
The two basic types of gear pumps are the internal, and the external. Both have an idler gear that is driven by the driving gear, and both use the same method to create pumping action, the gear coming in and out of mesh method. The main difference between the two types of gear pumps are where the fluid is trapped, and the placement of the gears.
There are no valves in a gear pump, or high impeller velocities, minimising the friction losses generally seen in a centrifugal-type pump.
With confidence Southern Pumping Specialists offers sound product knowledge of Gear pumps and the industries where they are applicable, as with the selection, sales, service and repair of these highly engineered items of equipment.
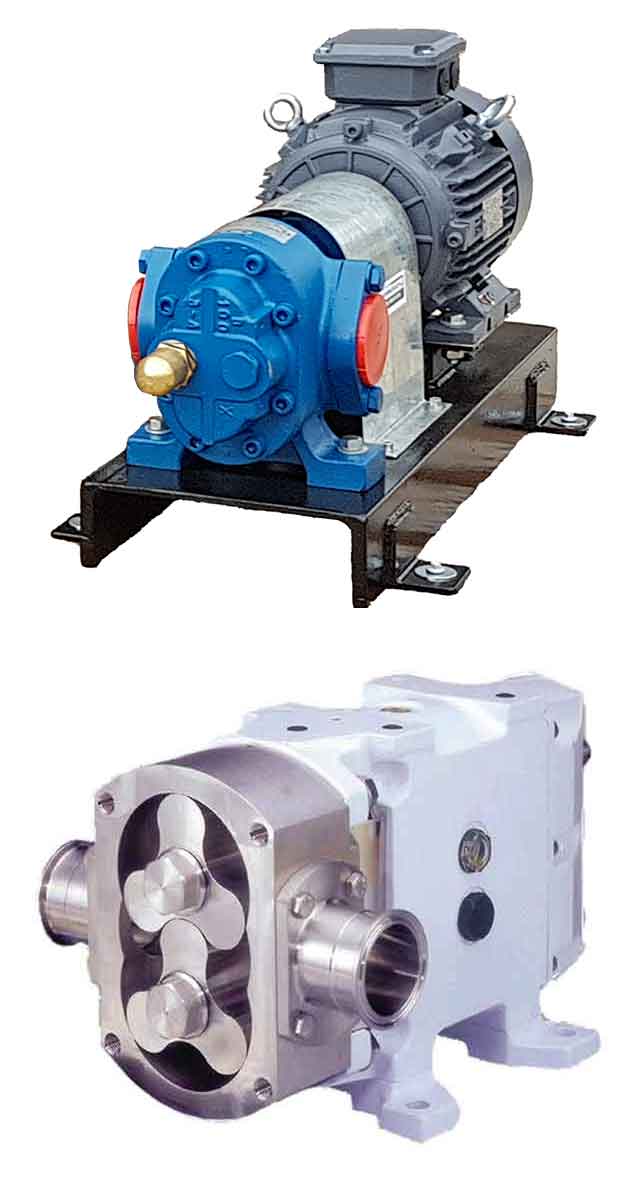
About the Haigh Pipeliner Macerator
The Pipeliner macerator fits into the suction line of raw sewage or sludge pump to homogenise the medium. This improves downstream process and protects high performance pumps from rag debris.
Its highly effective cutting action gives controlled particle size to eliminate the tendency of shredded solids to reform.
The self adjusting cutting assembly avoids the need for regular servicing and when maintenance is required the crucial wearing parts and be remove and replaced within minutes. See project details here.
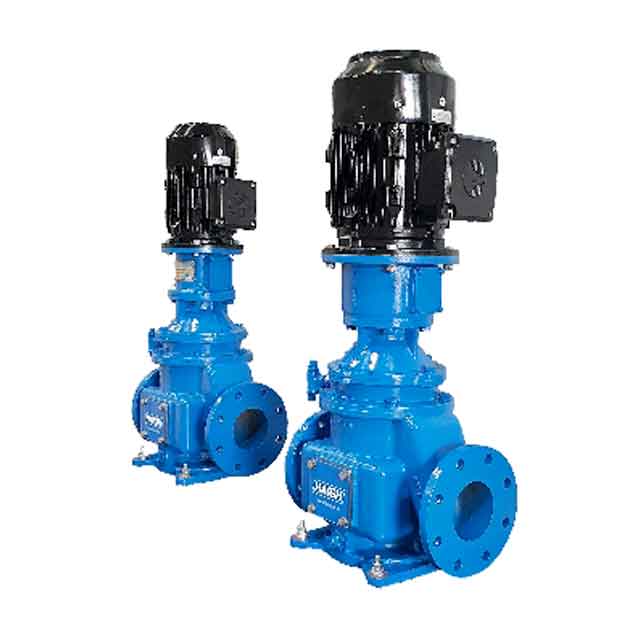
Helical Rotor pumps, also known as Progressive Cavity Pumps are a positive displacement principled pump. Simply a helical rotor rotates within a helically shaped rubber stator. The progressing cavity moves the liquid through the pump providing significant high head/pressure pumping advantage.
Helical Rotor Pumps are extensively used for moving sewage, slurries and other thick or viscous or solid fluids.
Southern Pumping Specialists has a dynamic offering of makes and models of Helical Rotor Pumps. These can be tailored to a specific application and built into complete pump sets with drive, gearbox etc. Spares are readily available and repairs are carried out with professionalism.
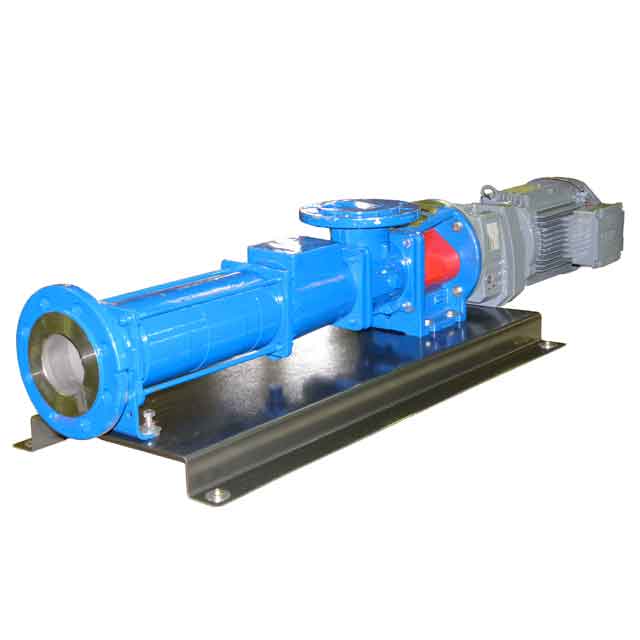
Southern Pumping has extensive knowledge in the supply and servicing of Magnetic Drive Pumps. A Magnetic Drive Pump eliminates the direct drive mechanism used in the traditional centrifugal pump, and replaces it with a magnetic field. It uses a balanced magnetic field to create the rotation of the fluid impeller.
These seal-less pumps are particularly suited to applications involving chemicals and other highly corrosive liquids that are unable to be pumped using a conventional pump with mechanical seal.
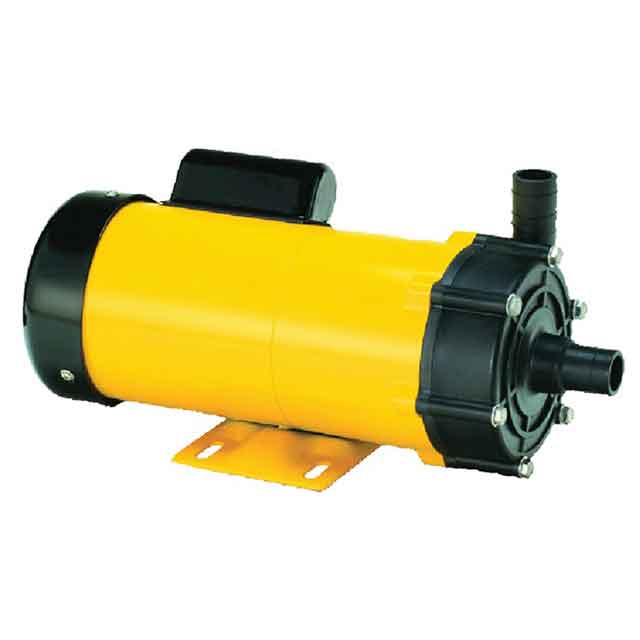
Types
Solenoid Metering Pumps
The output range of solenoid metering pumps ranges from 0.74 to 75 l/h and pressures to 16 - 20 bar. Metering pumps fulfil their metering tasks reliably,
even under the harshest operating conditions. Maintenance and repair costs are thereby extremely low. Thanks to the broad range of materials offered,
these metering pumps are suitable for practically all liquid chemicals.
Motor Driven Metering Pumps
Metering pumps with mechanically linked diaphragms are almost universally applicable in the low pressure range. They offer a favourable cost/performance
ratio at minimum service effort.
Process Metering Pumps
Process metering pumps are used in all applications where corrosive, toxic and flammable liquids are metered under very high pressures and extreme
temperatures. They are typically used in the chemical industry, petrochemical industry, refineries as well as oil and gas production or as special
metering pumps in the process industry.
Southern Pumping Specialists is ready to advise the most suited type of metering pump for any application along with the sales, spares and repairs of such pumps.
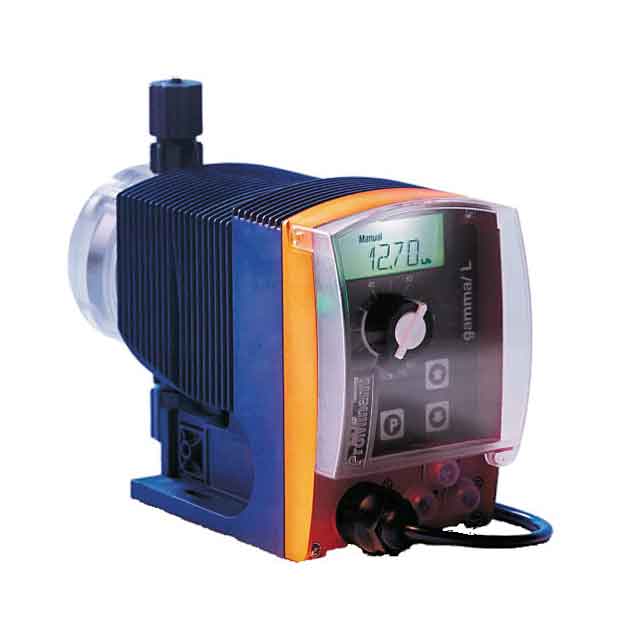
Peristaltic pumps provide excellent problem solving pumping solutions especially when the product being pumped is particularly abrasive, corrosive or viscous. Their lack of valves, seals and glands makes them inexpensive to maintain, the only maintenance item is the hose or tube. Peristaltic pumps also have a gentle pumping action, ideal for shear sensitive polymers and fragile cell cultures. Importantly, the only part of the pump in contact with the fluid being pumped is the interior of the tube or hose, making it easy to sterilise and clean the inside surfaces of the pump.
Southern Pumping Specialists has accumulated knowledge and experience in the selection, supply and repair of various makes of Perstaltic Pumps.
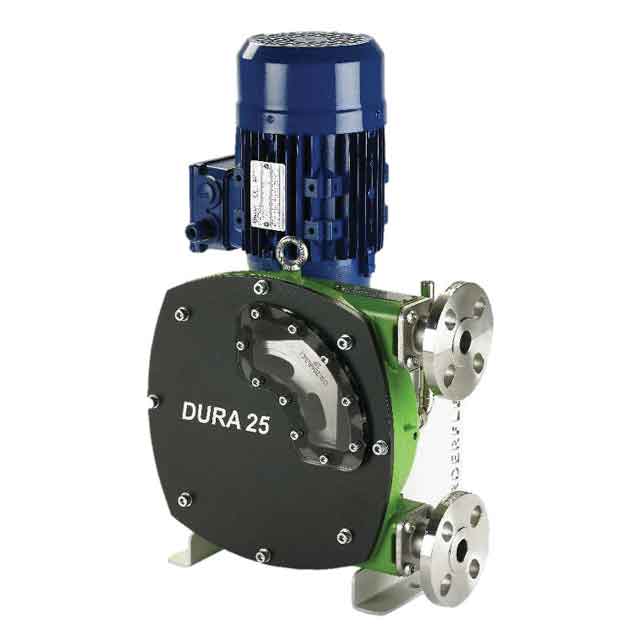
Heavy duty centrifugal slurry pumps designed for the continuous pumping of highly abrasive, high density slurries in mineral processing.
Whilst these pumps require minimal maintenance, the slurry pumps will maintain high efficiencies over the entire wear-life of their components.
With various construction configurations including vertical or horizontal, elastomer types, hardened metal options, engineered internal clearances and differing drive options these pumps are built to accommodate longevity with maximum abrasion and corrosion resistance in any application.
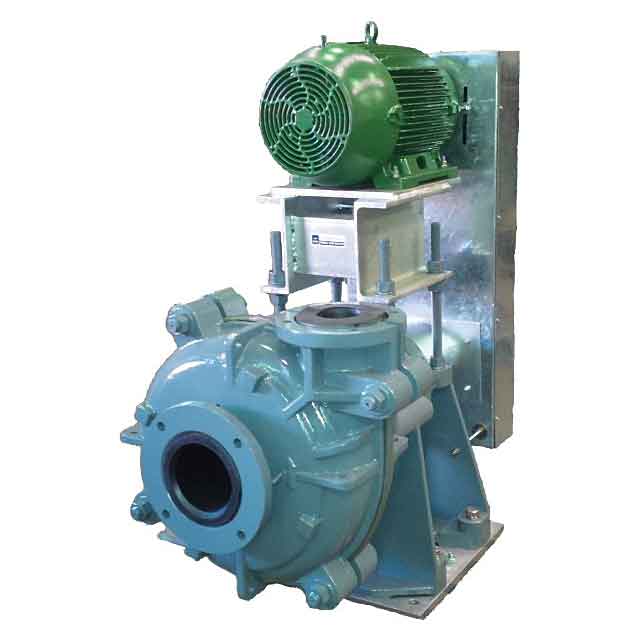
Submersible pumps are a common item of equipment that are available in many configurations to suit specific duties and applications.
Broadly, these versatile pumps are designed to operate with complete pump and motor submerged in the liquid they are pumping with the motor being cooled by the liquid being pumped.
A submersible pump is fitted with an impeller suited to a specific task. Some such impeller designs include; Vortex Impellers, Closed Impellers, Single Channel impellers, Multistage impellers and Cutter and Grinder mechanisms.
Other available options to be considered when selecting a submersible pump include; voltage, automatic/manual, high/low head, high/low flow, guide rail mounting, hazardous area pumps.
Southern Pumping Specialists has significant experience and service capacity along with a large inventory of pumps, spares and related products. The team is well qualified to assist with the selection, design and supply of a reliable submersible pump or system.
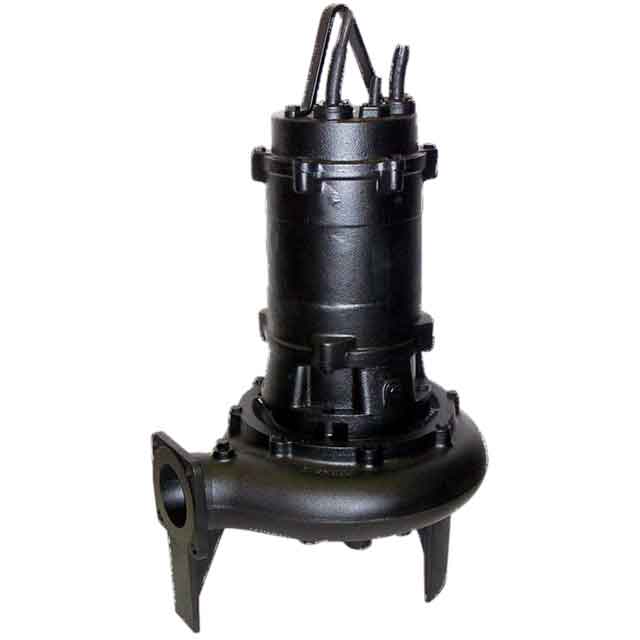
Vertical multistage pumps are applied to many applications. These versatile units are available in a number of different construction configurations including; cast iron, stainless steel, and titanium along with various shaft seal options, supply voltages and variable speed options.
There are up to twelve flow sizes, capable of producing up to almost 50 bar of pressure. The principle of multiple stages allows an increase to the output pressure relevant to the number of stages. Each stage contributes to the increases in the pressure as the fluid is led up through the stages then down the outside of the chamber stack to the outlet.
A single multistage pump can be an efficient and economical alternative replacing numerous conventional centrifugal pumps in series creating the required duty using these reliable pumps with relatively small footprints.
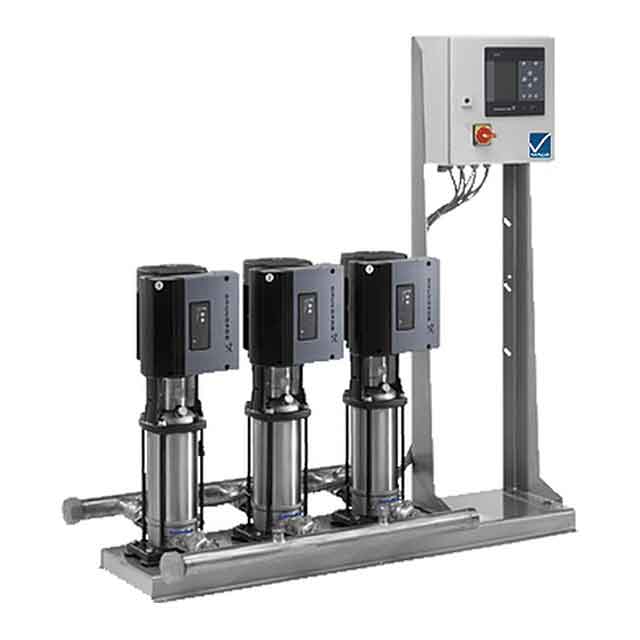