Pump Problems: Friction Loss
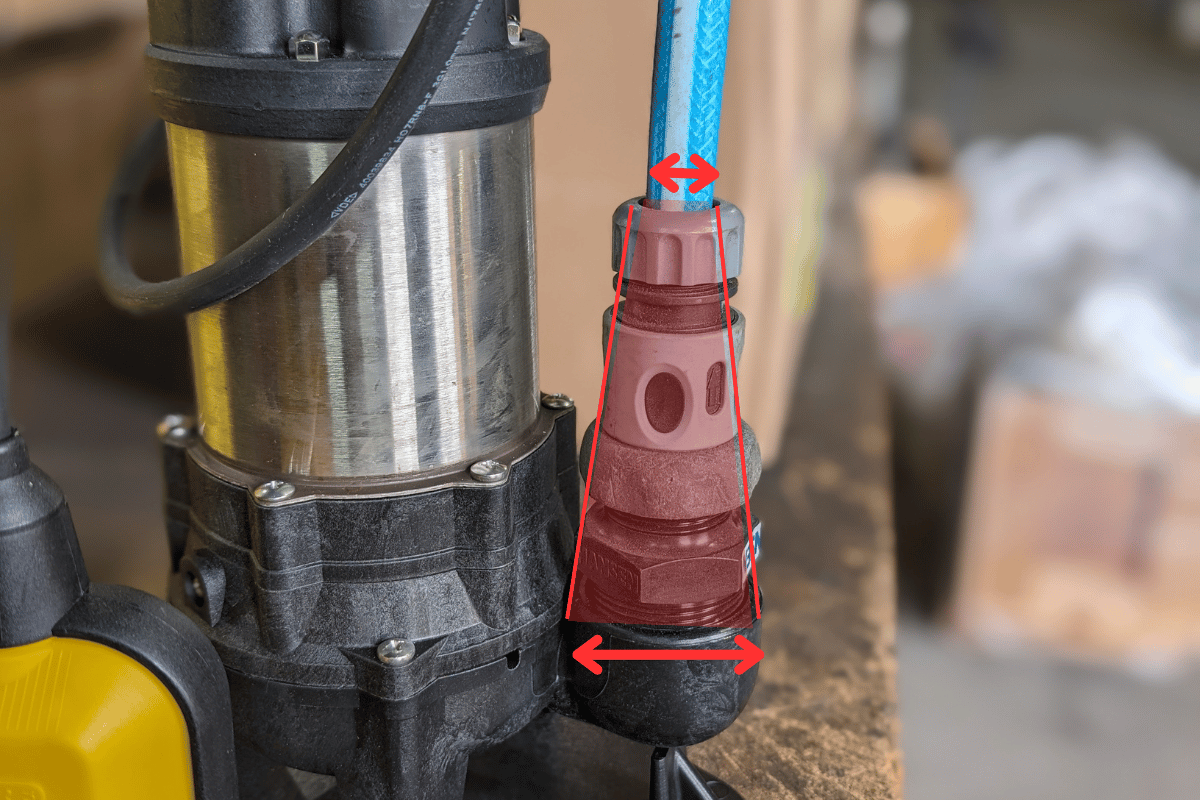
Friction loss occurs when fluid flowing through pipes encounters resistance, causing a drop in pressure and a decrease in flow rate. Understanding friction loss is key to optimizing the performance and energy efficiency of your pump system. By identifying the factors that contribute to friction loss, you can make informed decisions that will improve your system's overall effectiveness.
To truly grasp the concept of friction loss in pumping, it's essential to understand the basics of fluid dynamics. Fluids, such as water or oil, exhibit certain characteristics when in motion. These characteristics include viscosity, density, and velocity, all of which play a significant role in determining the amount of friction loss experienced in a pumping system.
Viscosity refers to a fluid's resistance to flow. Thick, syrup-like fluids have high viscosity, while thin, watery fluids have low viscosity. The higher the viscosity, the greater the friction loss. Density, on the other hand, is the mass per unit volume of a fluid. Denser fluids create more resistance and, consequently, more friction loss. Velocity is the speed at which fluid flows through the pipes. The faster the flow, the higher the friction loss.
Several factors contribute to friction loss in pumping systems. These factors can be broadly categorized into three main groups: pipe-related factors, fluid-related factors, and system-related factors.
Pipe-related factors include the diameter and length of the pipe, as well as the roughness of its inner surface. As a general rule, smaller pipe diameters and longer pipe lengths result in higher friction loss. Additionally, pipes with rougher inner surfaces create more resistance, leading to increased friction loss.
Fluid-related factors encompass the viscosity and density of the fluid being pumped. As mentioned earlier, higher viscosity and density lead to greater friction loss. The temperature of the fluid can also influence friction loss, with higher temperatures causing a decrease in viscosity and subsequently reducing friction loss.
System-related factors include the flow rate, pressure, and elevation changes within the pumping system. Higher flow rates and pressures increase friction loss, while elevation changes can either add to or subtract from it, depending on the direction of the change.
Calculating friction loss in pipes involves the use of empirical formulas, such as the Darcy-Weisbach equation or the Hazen-Williams equation. These equations take into account factors like fluid velocity, pipe diameter, and pipe roughness to determine the friction loss.
The Darcy-Weisbach equation is more accurate and widely used, as it accounts for the actual roughness of the pipe's inner surface. It is expressed as:
`hf = (f (L/D) (V^2/2g))`
Where:
- `hf` is the friction loss
- `f` is the friction factor
- `L` is the length of the pipe
- `D` is the diameter of the pipe
- `V` is the velocity of the fluid
- `g` is the acceleration due to gravity
On the other hand, the Hazen-Williams equation is simpler and often used for water flow calculations in municipal systems. It is expressed as:
`hf = (10.67 Q^1.85 C^-1.85 * D^-4.87)`
Where:
- `hf` is the friction loss
- `Q` is the flow rate
- `C` is the Hazen-Williams coefficient, which depends on the pipe material and roughness
- `D` is the diameter of the pipe
By using these equations, you can determine the amount of friction loss in your pumping system and make informed decisions to optimize its efficiency.
Pipe fittings, such as elbows, tees, and valves, introduce additional resistance to fluid flow, leading to increased friction loss. The impact of pipe fittings on friction loss depends on their shape, size, and the angle at which the fluid changes direction.
Elbows, for example, cause a significant increase in friction loss due to the abrupt change in flow direction. The greater the angle of the elbow, the higher the friction loss. Similarly, tees and valves also contribute to friction loss, albeit to a lesser extent.
It is crucial to consider the number and type of pipe fittings in your system's design to minimize friction loss. Opting for larger pipe diameters, using long-radius elbows instead of sharp ones, and strategically placing fittings can help reduce the overall impact on friction loss.
While friction loss is inevitable in pumping systems, there are several strategies you can employ to minimize its impact and optimize your system's efficiency.
The selection of an appropriate pump plays a crucial role in minimizing friction loss and optimizing system efficiency. Different pump types have varying characteristics that can impact friction loss.
Centrifugal pumps, for instance, are widely used due to their high efficiency and low friction loss. These pumps use impellers to generate centrifugal force, pushing fluid through the system. On the other hand, positive displacement pumps, such as piston or diaphragm pumps, can generate higher friction loss due to the pulsating flow they produce.
Factors to consider when selecting a pump include the required flow rate, pressure, fluid properties, and the desired overall efficiency. By choosing the right pump, you can minimize friction loss and achieve optimal performance for your pumping system.
Pipe wear can lead to increased friction loss.
Regular maintenance and troubleshooting are essential for reducing friction loss in pumping systems. Neglected or malfunctioning components can contribute to increased friction loss and decreased efficiency.
Some maintenance practices that can help mitigate friction loss include:
- Regularly inspecting and cleaning pipe surfaces to remove any buildup or corrosion that may increase roughness.
- Checking and repairing leaks, as they can disrupt fluid flow and increase friction loss.
- Lubricating moving parts to minimize resistance and improve overall system performance.
- Monitoring and adjusting flow rates and pressures to ensure optimal operation.
Troubleshooting should involve identifying and resolving any issues that may be causing excessive friction loss, such as improperly sized pipes, faulty valves, or inadequate pump selection. By addressing these issues promptly, you can significantly reduce friction loss and improve the efficiency of your pumping system.
Friction loss is an inherent characteristic of pumping systems that affects their efficiency and performance. By understanding the science behind friction loss, calculating its impact, and implementing strategies to minimize it, you can optimize your pump system's energy efficiency and save both time and money.
In this article, we explored the basics of fluid dynamics, the factors influencing friction loss, the methods to calculate it, and the strategies to minimize it. We also examined the impact of pipe fittings, the importance of pump selection, and the significance of maintenance and troubleshooting.
Armed with this knowledge and the tools provided, you can now confidently tackle friction loss in your pumping system. By making informed decisions, optimizing flow rates, and selecting appropriate equipment, you will maximize efficiency and achieve superior performance.
Remember, a thorough understanding of the science behind friction loss is the key to unlocking the full potential of your pumping system. Embrace this knowledge, apply it to your operations, and reap the benefits of an optimized and highly efficient pumping system.
Call us on (02) 4271 2220
email us here or complete the order form below