Pump Problems: Dry Run
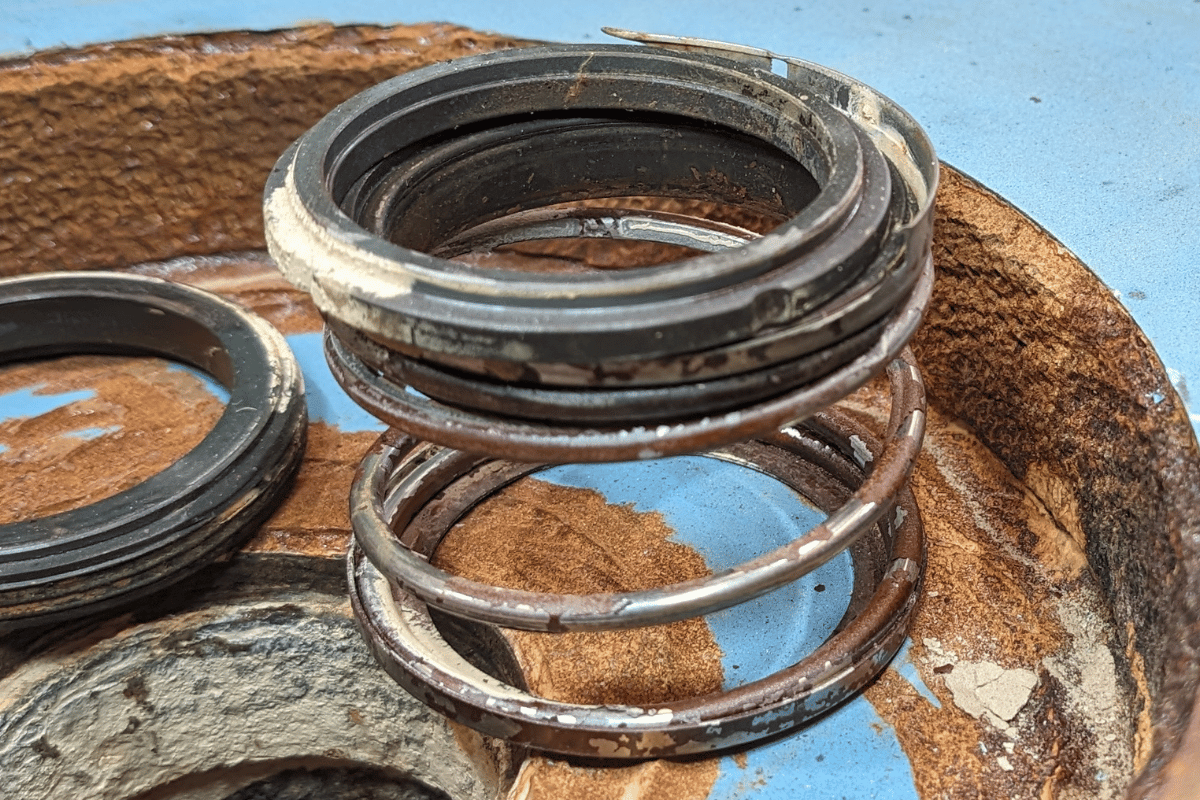
When a pump runs dry, it can lead to cavitation, overheating, which can lead to mechanical failures and even fires.Prevention is key when it comes to addressing dry run. Regular maintenance and inspections can help identify potential problems before they escalate. Implementing reliable monitoring systems and installing fail-safe mechanisms can also provide an added layer of protection.
Dry run can occur due to various reasons. One of the most common causes is a loss of prime, which happens when the pump loses its ability to draw or maintain liquid. This can occur when the pump is not properly primed before operation or when the liquid source is interrupted.
Another cause of dry run is a blocked or clogged inlet. If the pump's inlet is obstructed by debris or buildup, it can prevent the flow of liquid into the pump, leading to dry running. Similarly, a closed or partially closed valve can restrict the flow of liquid and result in dry run.
Furthermore, inadequate lubrication can also contribute to dry run pump problems. If the pump lacks sufficient lubrication, it can cause excessive friction and heat, leading to premature wear and failure. It is essential to ensure that the pump is properly lubricated to prevent dry running.
Detecting dry run early on is crucial to prevent further damage and downtime. There are several signs and symptoms that businesses should be aware of to identify these issues promptly.
One of the most noticeable signs of dry run is unusual noise coming from the pump. Cavitation can cause a distinct knocking or rattling sound, indicating that the pump is experiencing air or vapor bubbles collapsing. Additionally, overheating can cause the pump to emit a burning odor or smoke, which should be taken as a warning sign.
Another symptom of dry run is reduced or fluctuating flow rates. If the pump is not receiving a steady supply of liquid, it will struggle to maintain a consistent flow. Monitoring the flow rates and comparing them to the expected values can help identify potential dry run.
Visual inspection can also reveal signs of dry run pump problems. Look for signs of excessive wear or damage on the impeller, casing, or seals. Additionally, check for signs of leakage or abnormal vibrations, as these can indicate underlying issues with the pump.
Dry run can have a significant impact on equipment and processes. When a pump runs dry, it not only affects the pump itself but also other components and systems connected to it.
One of the primary impacts of dry run is reduced efficiency. When the pump is not operating optimally, it requires more energy to perform its intended function. This leads to increased energy consumption and higher operational costs. Additionally, reduced efficiency can result in decreased productivity and output.
Furthermore, dry run can cause damage to the pump and its components. Cavitation can erode the impeller and casing, leading to reduced performance and eventual failure. Overheating can cause seals to deteriorate, resulting in leaks and potential contamination. These damages can be costly to repair or replace and can result in extended downtime.
In some cases, dry run can also pose safety risks. Overheating can lead to mechanical failures, which can cause equipment malfunctions or even fires. This not only puts employees at risk but also jeopardizes the entire facility and its operations.
The dangers and risks associated with dry run extend beyond equipment damage and reduced efficiency. Addressing these issues is crucial to prevent more severe consequences that can impact the overall operation and safety of industrial processes.
One of the potential risks of dry run is the contamination of the pumped liquid. When a pump runs dry, it can introduce foreign particles into the system, compromising the quality and integrity of the liquid. This can have serious implications in industries such as food and pharmaceuticals, where product purity and safety are paramount.
Additionally, dry run can lead to the failure of critical processes or systems. If a pump failure occurs in a crucial stage of a production line, it can disrupt the entire operation and result in costly downtime. This can have severe financial implications for businesses, especially if they rely on continuous production or have strict deadlines to meet.
Moreover, dry run can cause environmental hazards. In industries that deal with hazardous or toxic liquids, a pump failure can result in leaks or spills, leading to environmental contamination and regulatory non-compliance. This can result in fines, legal consequences, and reputational damage.
Prevention is the key to avoiding dry run and their associated risks. By implementing preventive measures, businesses can minimize the occurrence of these issues and maintain the efficiency and reliability of their pump systems.
Regular maintenance and inspections are essential to identify and address potential problems before they escalate. Scheduled maintenance should include checking for signs of wear, leaks, or damage, as well as verifying proper lubrication and alignment. Inspections should also focus on ensuring that inlet lines are clear and valves are functioning correctly.
Implementing reliable monitoring systems can provide real-time data on pump performance and alert operators to potential issues. These systems can measure flow rates, pressure levels, and temperature, allowing businesses to detect abnormalities and take immediate action.
Installing fail-safe mechanisms can also provide an added layer of protection against dry run. Automatic shut-off valves can prevent dry running by stopping the pump when it detects a loss of prime or inadequate flow. Pressure relief valves can help alleviate excessive pressure and prevent cavitation.
Training employees on proper pump operation and maintenance is essential. By educating operators on the risks and consequences of dry run, businesses can ensure that they are equipped with the knowledge and skills to prevent these issues.
Regular maintenance and inspections are crucial to the longevity and efficiency of pump systems. By following a comprehensive maintenance schedule, businesses can minimize the risk of dry run and ensure the smooth operation of their processes.
Maintenance should include visual inspections, lubrication checks, and performance tests. During visual inspections, look for signs of wear, damage, or leakage. Lubrication checks should ensure that the pump is properly lubricated and that all moving parts are adequately protected. Performance tests should include verifying flow rates, pressure levels, and temperature readings.
In addition to regular maintenance, businesses should also conduct periodic inspections. These inspections involve a more in-depth evaluation of the pump system and its components. Inspect and clean the inlet lines, check the impeller and casing for signs of erosion or damage, and verify the integrity of seals and gaskets.
It is essential to keep detailed records of all maintenance and inspection activities. This allows businesses to track the history of their pump systems, identify recurring issues, and plan for future maintenance needs. By prioritizing regular maintenance and inspections, businesses can proactively address potential dry run and ensure the longevity and reliability of their systems.
Despite proactive measures, dry run can still occur. When these issues arise, it is crucial to take immediate action to prevent further damage and downtime. Troubleshooting and resolving dry run require a systematic approach.
The first step in troubleshooting is to identify the cause of the dry run issue. Check for any loss of prime, blocked inlets, closed valves, or inadequate lubrication. Addressing the root cause is essential to prevent the issue from recurring.
Once the cause is identified, take the necessary actions to resolve the dry run pump issue. If there is a loss of prime, ensure that the pump is properly primed. If the inlet is blocked, clear the obstruction or clean the inlet lines. Open any closed valves or adjust them to allow for proper flow. Finally, ensure that the pump is adequately lubricated to reduce friction and heat.
After resolving the issue, monitor the pump closely to ensure that it is operating correctly. Keep an eye on flow rates, pressure levels, and temperature readings to verify that the pump is functioning within the desired parameters.
While regular maintenance and inspections play a significant role in preventing dry run, it is also essential to engage professional pump services. Professional pump services have the expertise and experience to assess, maintain, and repair pump systems effectively.
Professional pump services can provide comprehensive inspections and maintenance that go beyond regular activities. They have the knowledge to identify potential issues before they become problems and can recommend appropriate actions to prevent dry run.
In case of pump failures or more complex issues, professional pump services can offer prompt and efficient repairs. They have the necessary tools and equipment to diagnose and resolve problems quickly, minimizing downtime and ensuring the smooth operation of industrial processes.
By relying on professional pump services, businesses can benefit from the expertise and specialized knowledge of professionals in the field. This allows them to focus on their core operations while ensuring the reliability and efficiency of their pump systems.
Dry run may seem insignificant, but they can have severe consequences for industrial operations. From reduced efficiency to equipment damage and safety risks, neglecting these issues can result in costly downtime and potential hazards.
Prevention is key when it comes to addressing dry run. Regular maintenance and inspections, reliable monitoring systems, and fail-safe mechanisms are essential to minimize the occurrence of these issues. Training employees on proper pump operation and maintenance is also crucial.
By understanding the risks and dangers associated with dry run, businesses can prioritize preventive measures and ensure the reliability and efficiency of their operations. Engaging professional pump services can provide additional support and expertise.
In conclusion, businesses must not underestimate the silent danger of dry run. By taking the necessary precautions and investing in proactive maintenance, they can avoid costly disruptions and maintain the longevity of their pump systems.
Key Takeaways:
Call us on (02) 4271 2220
email us here or complete the order form below