Pump Problems: Cavitation
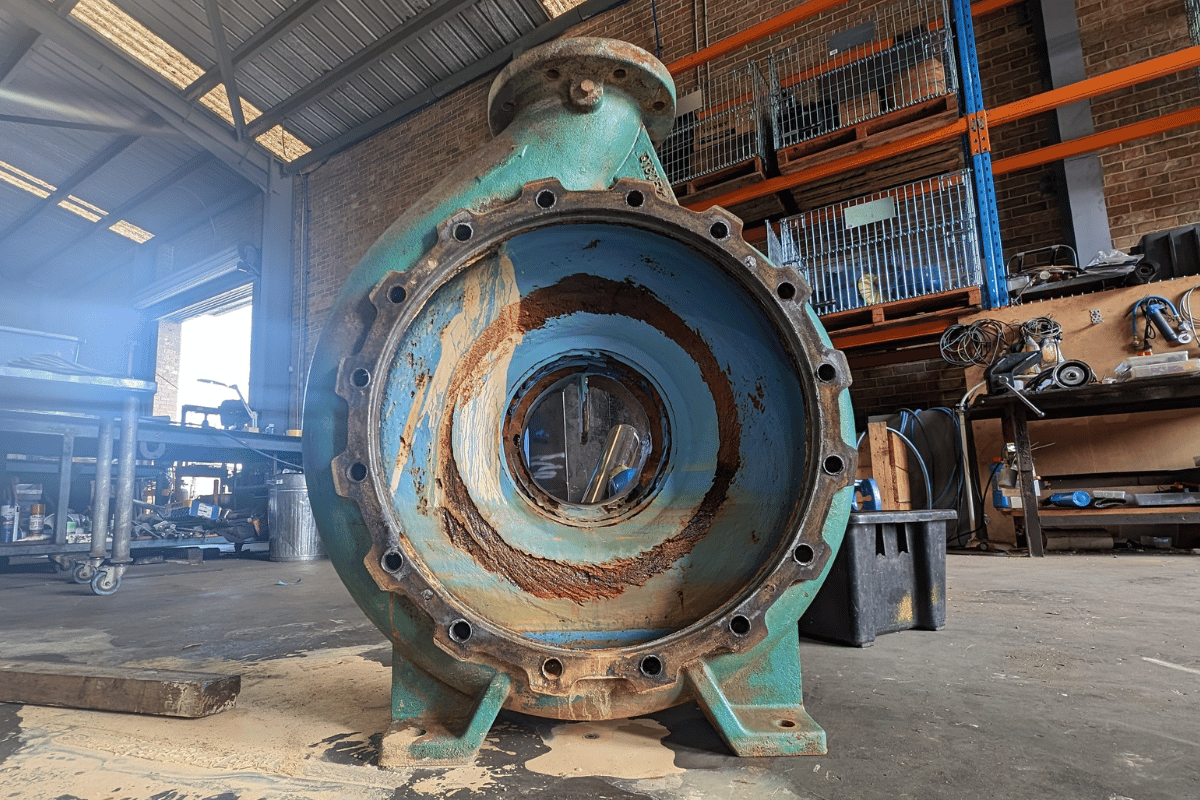
Cavitation happens when the pressure in a pump drops sufficiently, causing the liquid to vaporize and form bubbles. These bubbles are not as innocent as they sound; upon collapsing, they can generate shockwaves potent enough to erode the pump's impeller and other components. This results in reduced flow, efficiency, and potentially, catastrophic failures. Cavitation is not just about the bubbles; it's about the velocity at which liquid moves, creating low-pressure regions prone to vapor bubble formation. These regions, especially prevalent in centrifugal pumps and water turbines, can see air bubbles becoming as corrosive as sand, wearing down the pump casing and, in extreme cases, puncturing holes even in cast iron.
A frequent culprit behind cavitation is an inadequately fed suction line or the presence of holes in the suction line, which introduces air into the system. Addressing this involves increasing the pressure upstream from the pump’s impeller. This could mean upsizing the suction line or ensuring it's free from holes, blockages, or any air inlets. Inspecting and possibly rectifying issues in the suction line and the foot valve can significantly mitigate cavitation risks.
Cavitation isn't silent; it often announces its presence through noises that resemble gravel or marbles coursing through the system. Besides the audible warnings, vibration, reduced flow rates, and a drop in pump efficiency are common indicators. The aftermath of cavitation extends beyond noise, leading to wear on seals, o-rings, and bearings, which may cause leaks and pressure loss. Notably, centrifugal pumps bear the brunt of damage with the impeller and pump housing succumbing to the erosive force of air bubbles, alongside an uptick in power consumption due to the added strain on the pump.
The advancements in cavitation prevention are promising, offering several technologies and methodologies to safeguard your system. Variable Speed Drives (VSDs) and Computational Fluid Dynamics (CFD) modelling stand out by enabling precise control over pump operation and simulating fluid dynamics to preemptively address potential cavitation zones. Furthermore, the evolution in pump impeller designs and the use of resilient materials fortify the pump's defences against cavitation-related damage.
Processes to mitigate the damaging effects of cavitation include ceramic coating or heat treating the pump components to protect them from abrasive cavitation bubbles. These specialist processes can be done on site at Southern Pumping.
Addressing cavitation damage effectively can involve repairing or replacing the affected impeller, installing wear rings or sleeves to shield the impeller and pump casing, or, in severe cases, overhauling or replacing the pump. Proactive measures, coupled with these remedies, can significantly extend the life and efficiency of your pumping system.
Navigating through the complexities of cavitation no longer has to be a daunting task. With a thorough understanding of cavitation's causes, signs, and effects, complemented by the latest in prevention technologies and effective remedies, you can turn the tide against this pervasive issue. Embrace these strategies to not just mitigate cavitation but to enhance the overall performance and reliability of your pumping system. Your commitment to proactive maintenance and innovation paves the way for a more efficient, durable, and cost-effective operation. Here's to the smooth running of your pumps, free from the setbacks of cavitation!
Call us on (02) 4271 2220
email us here or complete the order form below