Pump Problems: Airlock
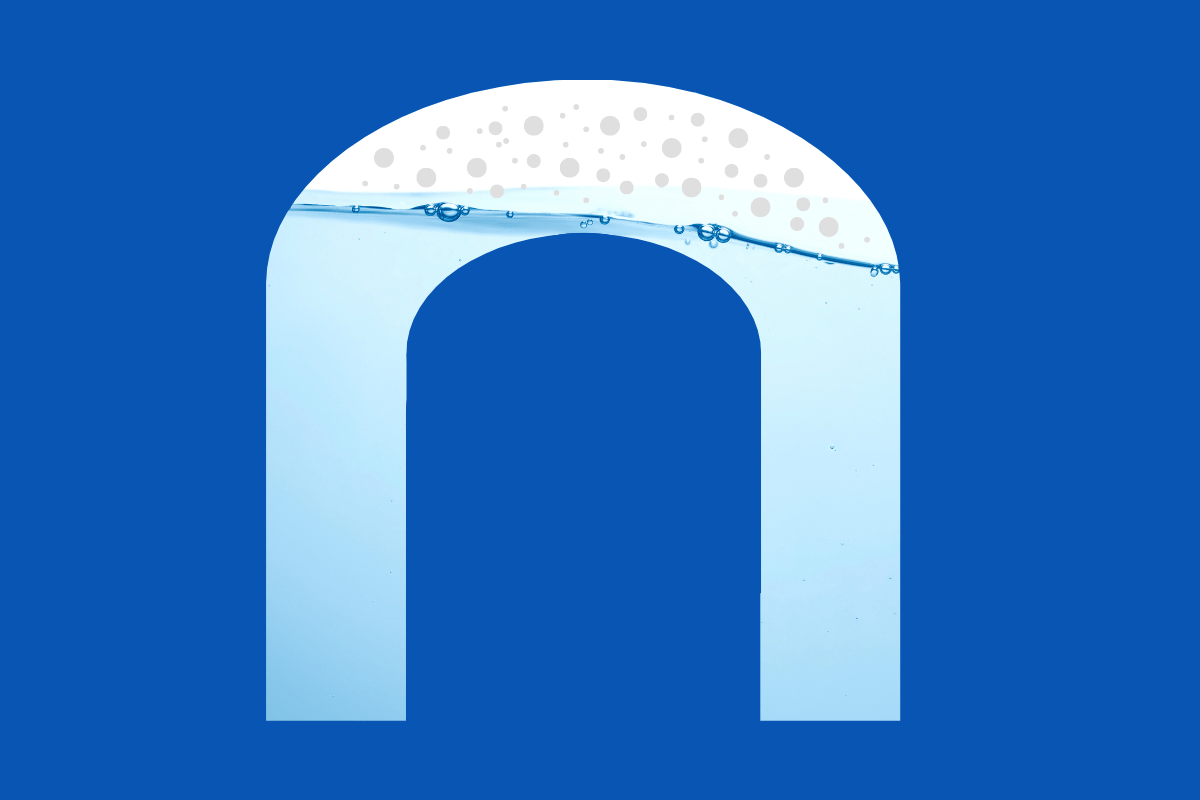
Airlock can occur in various types of pumps, and understanding its root causes is crucial for preventing it. Here are the primary causes:
- Inadequate Priming: When a pump is not properly primed, meaning the suction line and pump casing are not filled with liquid, air can be drawn into the system, leading to airlock.
- Suction Line Leaks: Cracks, holes, or loose connections in the suction line can allow air to enter the system, preventing the pump from functioning correctly. These issues may arise from wear and tear, improper installation, or system configuration changes.
- Improper Pump Installation: Incorrect installation, such as misalignment of the suction line or an unlevel pump, can create air pockets, leading to airlock.
Identifying airlock in a pump involves looking for several telltale signs:
- Loss of Suction or Flow: The pump may appear to be running but fails to draw in or move the liquid effectively. This often comes with a noticeable reduction in discharge pressure.
- Cavitation: Occurs when the pump can't fill the impeller with liquid, causing air bubbles to form. This can lead to vibrations, noise, and damage to the pump's internal components over time.
- Overheating: Trapped air reduces the pump's ability to cool itself, potentially causing overheating and further damage.
Airlock can significantly affect a pump’s performance and efficiency by decreasing suction and flow. When air gets trapped in the pump, it hampers its ability to draw in and move liquid effectively, leading to reduced discharge pressure and diminished performance. This inefficiency forces the pump to work harder, resulting in increased energy consumption, higher operating costs, and a shortened lifespan. Additionally, the presence of airlock can cause vibrations and stresses within the pump, accelerating wear and tear on internal components, thereby raising the risk of premature failure and expensive repairs.
To prevent airlock, a proactive approach is necessary. Ensuring proper priming before startup by filling the suction line and pump casing with liquid helps eliminate air pockets. Regular inspection and maintenance of suction lines are crucial; checking for cracks, holes, or loose connections and addressing any issues promptly can mitigate the risk of airlock. Moreover, proper installation practices, such as installing pumps level and ensuring correctly aligned suction lines, are essential. Using appropriate pipe fittings and valves also helps prevent air leaks, thus avoiding the formation of air pockets in the system.
If airlock does occur, follow these steps to troubleshoot and resolve the issue:
1. Check for Leaks: Inspect the suction line for leaks or obstructions that could allow air into the system.
2. Verify Priming: Ensure the priming system functions correctly, which may involve manual priming or checking components like the priming valve.
3. Inspect Internal Components: If airlock persists, examine the pump's impeller and other internal parts for damage or wear.
Here are some expert tips for managing and preventing airlock:
- Regular Inspections: Conduct routine checks of pumps, suction lines, and priming systems.
- Proper Installation: Follow manufacturer instructions for installation, ensuring proper alignment and avoiding air pockets.
- Robust Priming Process: Develop a standardized priming procedure and train operators to prevent airlock.
- Performance Monitoring: Keep track of pump performance metrics to detect early signs of airlock.
- Consult Experts: Seek advice from pump experts or manufacturers if facing persistent airlock issues.
Airlock in pumps is a common issue with serious consequences, from reduced efficiency and increased costs to production downtime. By understanding its causes, implementing preventive measures, and maintaining regular inspections, you can minimize the risk of airlock and ensure reliable pump performance. Stay proactive and vigilant to protect your operations from costly breakdowns and maintain a competitive edge in your industry.
Call us on (02) 4271 2220
email us here or complete the order form below