Overhaul of Warman 100RV SP Pump
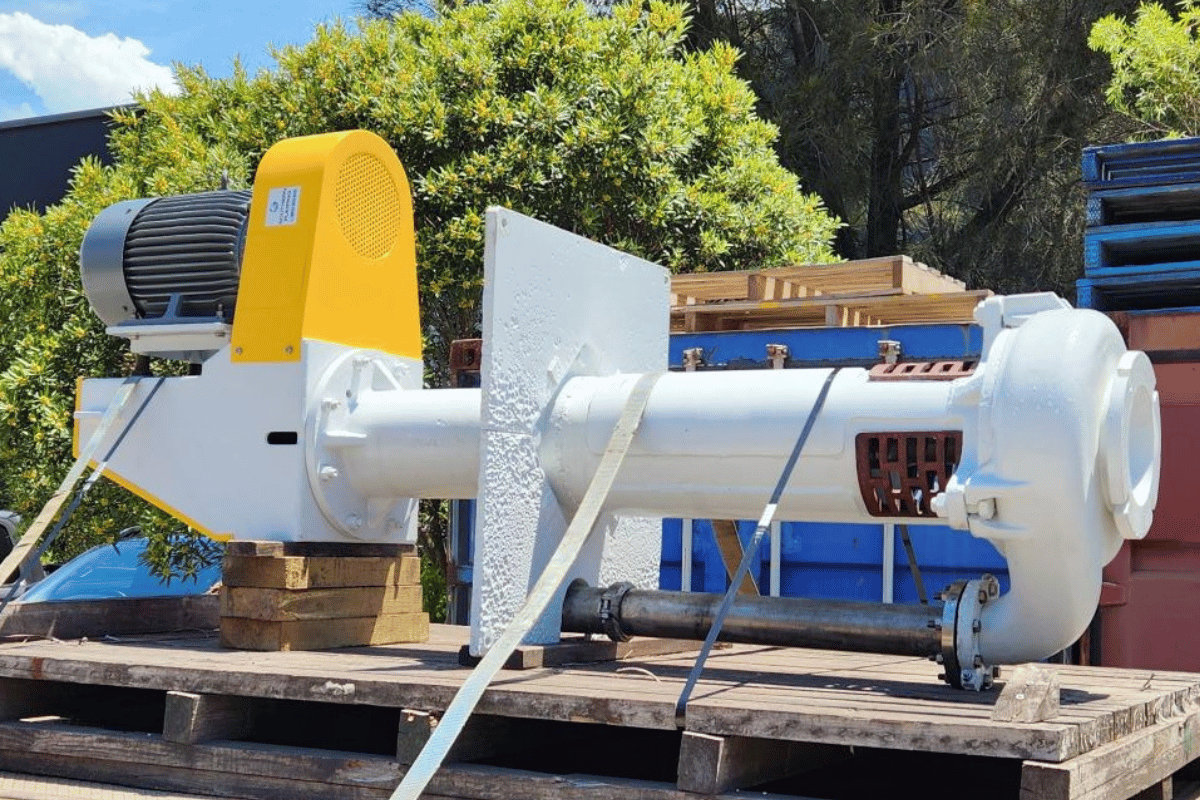
The pump arrived at our workshop bearing the scars of its demanding service life. Heavy rust and corrosion covered the column and guards, bearings were caked in excess grease, and a large rock had wedged itself in the discharge. Despite these issues, the pump’s high-chrome impeller and casings hinted at its potential for rejuvenation.
Heavy rust and corrosion were observed on the column and guards, accompanied by excess grease deposits in the bearings. A large rock obstructing the discharge highlighted the need for thorough cleaning and assessment.
Key Component Observations:
Additional Findings:
Repair Recommendations:
External Work:
The motor was removed at the client's request and sent to Arrow Electrical for inspection and repair.
This project demonstrated the power of combining advanced cleaning techniques, strategic repairs, and regulatory-driven upgrades to breathe new life into aging equipment. Southern Pumping’s tailored approach ensured that the Warman 100RV slurry pump was ready to perform when needed, minimizing downtime and maximizing operational efficiency.
This pump’s story is far from over—it’s set to write a new chapter of reliability and resilience in one of Australia’s most demanding industrial environments.
Call us on (02) 4271 2220
email us here or complete the order form below